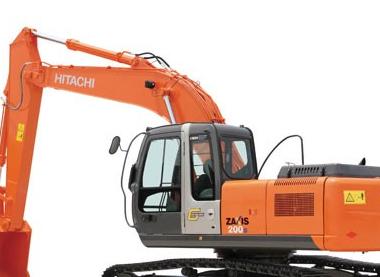
On the one hand, “adjustment of structure†of construction machinery represents the adjustment of product structure. That is, through the adjustment of the current round, product types and product models will be more complete. Any project that requires operations can find corresponding construction machinery to replace manual work. On the other hand, the composition of enterprises in the construction machinery industry has been adjusted. Through this round of "freezing period" adjustment, a large number of small and medium-sized enterprises will withdraw from the construction machinery industry or be annexed.
The "turning mode" of construction machinery also manifests itself in two aspects:
First, in order to transform the single approach to the domestic market, large-scale enterprises are increasingly turning to the international market for operations, and they have globally placed production, operations, services, and capital operations;
Second, change the single focus on the market before the product, and pay more attention to the aftermarket of the product, including technical services, sales of accessories, second-hand mobile phone transactions, leasing, and remanufacturing.
As far as after-sale technical services are concerned, the "advanced service" model will be the choice of the scientific operating model for the introduction, absorption, and digestion of China's construction machinery industry.
Why did you propose the "advanced service" model? After the user completed the construction machinery product transaction, the tangible physical property rights of the construction machinery were transferred. If the user made a one-time payment, the tangible property rights of the construction machinery were directly transferred to the user, and the credit sales were transferred to the financial institution. However, the brand of intangible assets construction machinery is always owned by the enterprise during the entire life cycle of the construction machinery. In this sense, the enterprise has the responsibility to manage the construction machinery of the enterprise brand purchased by the users in coordination with the users. This is the starting point for proposing the "advanced service" model.
A notable feature of modern equipment management in China is to emphasize the systematic management of equipment during the entire life cycle of equipment planning, design, manufacturing, sales, installation, commissioning, function, maintenance, renewal, and remanufacturing (rejection). Specifically, it is “five combinationsâ€: the combination of design, manufacture and use; the combination of maintenance and repair; the combination of repair, transformation, and renewal; the combination of professional management and mass management; and the combination of technical management and economic management. At the same time there are also "five management": full-benefit management goals; the entire process of management; full participation in the management of organizations; all means of management technology; the entire community management cycle. Among them, "combination of design, manufacturing and use" means that enterprises should participate in the use management of users, users should participate in the design and manufacturing management of enterprises, and "the whole society management cycle" includes equipment use management microcirculation, equipment life management cycle, Equipment industry management cycle and equipment social management cycle. Among them, "the equipment life management minor cycle" refers to the enterprise to participate in the management of the second half of the equipment, users must participate in the management of the first half of the equipment. This is the theoretical source of the "advanced service" model.
At present, the relationship between enterprises and users has evolved from a traditional trading relationship to a partnership. This is an objective basis for proposing the "advanced service" model.
The widespread use of GPS-centric IT technology in construction machinery products has realized the interconnection of people and machinery, machinery and machinery, and people, which is the technical prerequisite for the "advanced service" model.
The concept of "advanced service" construction machinery as a tangible type of fixed assets for production, generally shows four characteristics: technical characteristics, economic characteristics, brand characteristics and information characteristics. After a user purchases a construction machine, he must implement technical management, economic management, brand management, and information management for the construction machine in order to achieve the most economical life cycle cost of the construction machine and the highest comprehensive efficiency. After the construction machinery is sold, the company sends technical service personnel to participate in the above management in coordination with users. This is the advanced service mode of construction machinery.
Therefore, "advanced service" for construction machinery can be defined as: enterprise technical service personnel collaborate with users to manage the construction machinery purchased by users.
In the above definition, first look at the concept of "collaboration." Collaboration is the abbreviation of "Synergy Effect". The synergistic effect is originally a kind of physical and chemical phenomenon, also called synergism. It means that two or more components are added or blended together, and the effect produced is greater than the sum of the effects of each component when used alone. "Synergies" are applied to advanced services, which means that users and enterprise service personnel work together to manage machines, and they will obtain better investment returns.
The next question is whether the user accepts the enterprise service personnel to collaboratively manage the machines he purchases. As mentioned in the context of advanced services, after the user completes the purchase of the construction machinery transaction, although the physical assets equity has been transferred, the intangible asset manufacturing company brand Throughout the entire life cycle of construction machinery, in this sense, as the engineering machinery consisting of physical (tangible) assets and intangible assets, the value of its intangible assets is much greater than that of physical assets. Therefore, the concept of “shares†is used. For a tangible and intangible construction machinery asset, a company is in a “controlling position†and is a “major shareholderâ€. Therefore, the technical service personnel sent by the company not only have the right to coordinate users to manage the machines purchased by users, but also users need to follow the requirements of the technical service personnel and do the following three requirements: first, correct operation; second, strict maintenance; Third, purchase the designated consumables.
This is a subversion of advanced services to the relationship between traditional users and businesses. According to the concept of traditional Chinese culture, users are the food and clothing parents of the company. According to the concept of Western culture, users are the God of the company. Whether it is “parents†or “Godâ€, the conclusion is that enterprises must unconditionally listen to users, while advanced services emphasize that Users should obey the enterprise technical service personnel! Technical service personnel are no longer repairmen, but “supervisors,†“finance engineers,†and “small bosses.†These sold machines have become a source of profit for companies in the post-market.
Advanced service technology management is centered on the "failure" of construction machinery to prevent failures and reduce failures. Once failures occur, mechanical functions are restored in the shortest possible time. To this end, advanced services require users (operators) to properly operate the machinery and strictly maintain the machinery in accordance with the mechanical operation and maintenance manuals. Enterprises (technical service personnel) collaborate with users to maintain and repair machinery.
The advanced service economic management is based on the life cycle cost of construction machinery, and dynamically evaluates the value of machinery, providing reference for users in the process of mechanical overhaul, modification, and update. Enterprises (technical service personnel) provide mechanical economic evaluation reports for users on a monthly, quarterly, and annual basis, and propose plans for retention, repairs, alterations, updates, and improvements.
Advanced service information management is the basis and means of technology management, economic management, and brand management. It adopts GPS technology as the core IT technology configured by construction machinery to obtain information on the status, maintenance and repair of machinery, and fuel consumption information in real time. , Job information and mechanical location information.
Advanced service brand management is the process through which companies (technical service personnel) and users interact to enhance brand value, achieve customer satisfaction, and create loyal customers.
Conditions for the implementation of advanced services Engineering machinery should be equipped with IT-centric IT technology, ie, Internet of things technology. This enables the enterprise (technical service personnel) to grasp the technology, economy, operation, location, etc. of the sold machinery at any time and anywhere through mobile phones and computer terminals so that the users can manage the construction machinery in coordination.
There is a higher demand for enterprise technical service personnel. Technical service personnel must not only be skilled, but also have the knowledge and methods for economic evaluation, but must also have superb communication skills. Specifically, the "three sessions": will do, speak, write. "Six Diligence": mouth diligence, hands diligence, feet diligence, ear diligence, brain diligence.
Enterprises should establish advanced service organization systems and mechanisms. The core of the implementation of advanced services for enterprises is the establishment of advanced service teams. The group is generally composed of 3 to 5 people, each responsible for managing 20 to 30 machines. Each group is equipped with a technical service car, technical service vehicles equipped with on-site mechanical state detection instruments, microcomputers, communication tools, and spare parts. Each advanced service group is a self-directed business entity that directly faces users. The responsibilities of the advanced service group are shown in Table 1.
In this way, an "inverted triangle" organizational structure is formed between the advanced service group, agents, and manufacturing companies, as shown in Figure 1. The new machine of the manufacturing company commissions the agent to operate within the specified area. The agent commissions the advanced service team to sell the machine to operate on the designated user, that is, to coordinate the user to manage these machines. In essence, the relationship between manufacturing companies and agents, agents, and advanced service groups is consistent. Therefore, advanced services believe that enterprise technical service personnel are "small bosses."
In fact, the sales staff expands the market for potential users, and the advanced service team consolidates the market for users.
Advanced service team remuneration and the profits of enterprises and agents come from the machines that the advanced service team manages collaboratively. Through the advanced service team's work, users, advanced service team members, agents, and manufacturers can “win togetherâ€.
6 Burners Electric Oven,Gas Stove With Hot Plate,Household Stainless Steel Gas Oven,Freestanding Gas Oven For Baking
Jiangmen Minsheng Kitchen Equipment Co.,Ltd , https://www.minshengchina.com