Internal clearance in ball and roller bearings refers to the amount of movement that occurs between the inner and outer rings when one is held fixed. This small but crucial space allows for smooth operation and accommodates changes due to temperature, load, and wear over time. Proper clearance directly affects a bearing’s performance, lifespan, and overall reliability.
In this article, we’ll explore what internal clearance means, why it's important, and how to choose the right clearance for your specific application. Understanding this concept can help you avoid premature failure and optimize the efficiency of your machinery.
Why Is Internal Clearance Important?
Bearing internal clearance plays a key role in ensuring efficient and reliable operation. It determines how the rolling elements (balls or rollers) interact with the raceways inside the bearing. If the clearance is too tight, it may cause excessive friction, heat, and wear. On the other hand, if it's too loose, it can lead to vibration, noise, and reduced load capacity.
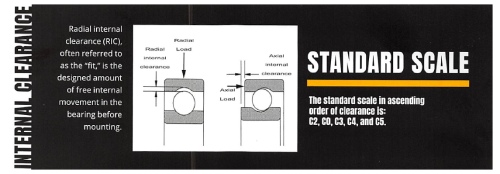
There are two main types of internal clearance:
- Radial Clearance – The distance between the inner and outer rings measured perpendicular to the bearing axis.
- Axial Clearance – The movement along the bearing axis, typically about ten times the radial clearance.
Calculating radial clearance involves subtracting the average inner raceway diameter from the outer one and adjusting for the size of the rolling elements. Axial clearance is generally larger and plays a significant role in high-speed or high-temperature applications where thermal expansion is a concern.
What Are the Ideal Clearance Levels?
The ideal internal clearance should be as minimal as possible, often just a few microns, to ensure optimal performance. However, the exact clearance required depends on several factors, including:
- Application type (e.g., industrial, automotive, aerospace)
- Operating temperature
- Load conditions (light, medium, heavy)
Choosing the right clearance ensures that the bearing can handle the stresses of its environment without failing prematurely. It also helps maintain smooth operation, reduce noise, and extend the service life of the bearing.
Related Reading:
- Friction Vs. Anti-Friction Bearings
Understanding C0 vs. C3 Clearances
When selecting a bearing, you may come across different clearance classes, such as C0 and C3. Here's what they mean:
- C0 (or CN): This is the standard clearance used in most general-purpose applications. It’s suitable for normal operating conditions and recommended fits. It’s usually not marked on the bearing itself.
- C3: This clearance is slightly larger than C0 and is used in situations where thermal expansion or special load conditions require more space. It’s commonly found in high-speed or high-temperature environments.
Each clearance type has its own advantages, and the right choice depends on the specific needs of your system. Using C3 clearance, for example, can prevent binding or damage caused by heat expansion, making it ideal for demanding applications.
Why Choose Emerson Bearing?
At Emerson Bearing, we specialize in producing precision-machined bearings designed for a wide range of industries. With decades of experience and a commitment to quality, we provide reliable solutions that meet the highest standards of performance and durability.
Our product line includes ball bearings, ceramic bearings, roller bearings, linear motion bearings, and super precision bearings, all engineered to deliver exceptional results in even the most challenging environments.
Whether you need custom solutions or standard components, our team is here to help. Contact us today via our Contact Us page or fill out our Request a Quote form to get started. We’re dedicated to delivering the precision and quality you need for your operations.
Peek Granules,Peek Medical Material,Astm Peek Granules,Peek Granules Medical Material
TMT INDUSTRY , https://www.tmtmedtech.com